Introduction to Central Feeding System The central feeding system is designed for the production of plastic products in the injection molding workshop, realizing uninterrupted unmanned continuous molding operations. The system can regenerate and use the nozzle cold material in a fully automatic way, can control all the feeding equipment, and prevent the occurrence of blockage in the storage bin, and realize full automation by setting up a central monitoring station. The central centralized feeding system adopts the centralized automatic control of the microcomputer to realize the continuous feeding operation of pellets for 24 hours. Multiple small microcomputers respectively control the coloring process of each molding machine, the measurement is accurate, the mixing is uniform, and the color can be flexibly changed to meet the requirements of multiple colors and varieties of products. According to the production capacity of different molding machines, the feeding amount can be flexibly changed. The design of multiple feed pipes can ensure the diversified requirements of the main materials. The system has a variety of monitoring and protection functions, and the work is safe and reliable. The aliases of the central feeding system are: centralized feeding system, automatic feeding system, etc. Central feeding system principle The central feeding system adopts a vacuum conveying method. The plastic raw materials are transported from the storage tank to the central dehumidification and drying system through a centralized pipeline system, and then the dried raw materials are transported to each injection molding machine. The central feeding system adopts the design method of "one machine, one pipe" to ensure that the air in the entire system transports the raw materials and prevent the raw materials from regaining moisture after dehumidification and drying. At the same time, each conveying operation is stable, and there is no material blocking phenomenon. It is used in conjunction with the central dehumidification and drying system. The conveying pipeline can be cleaned after the dehumidification and drying cycle to ensure that there are no residual pellets in the pipeline. While avoiding the regain of the raw materials, it also ensures the performance of the raw materials added to the injection molding machine. Consistent. Under the action of vacuum negative pressure, the original dust in the raw material will be filtered out through the dust filter system, which helps to improve the quality of the molded product. At the same time, each conveying operation is stable, and there is no material blocking phenomenon. It is used in conjunction with the central dehumidification and drying system. The conveying pipeline can be cleaned after the dehumidification and drying cycle to ensure that there are no residual pellets in the pipeline. While avoiding the regain of the raw materials, it also ensures the performance of the raw materials added to the injection molding machine. Consistent. Under the action of vacuum negative pressure, the original dust in the raw material will be filtered out through the dust filter system, which helps to improve the quality of the molded product. The composition of the central feeding system
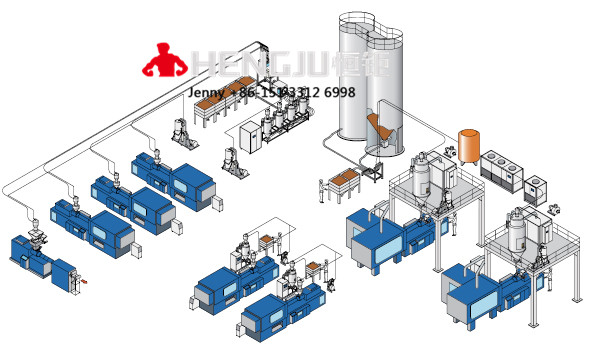 Central console, cyclone dust collector, high-efficiency filter, fan, branch station, drying hopper, dehumidifier, material selection rack, micro-motion hopper, electric eye hopper, air shutoff valve, shutoff valve. Features of central feeding system 1. Efficient: The central feeding system can automatically supply a variety of raw materials to any injection molding processing equipment in multiple chambers, which can include drying treatment of raw materials, color matching treatment, and proportional utilization of crushed recycled materials, which can achieve high Automatic control, monitoring, etc., and can meet the production needs of 24 hours non-stop. 2. Energy saving: The central feeding system is easy to operate, and only a few people are needed to control the feeding demand of the entire injection molding plant, thereby reducing a lot of labor costs. Secondly, the raw material belt and the corresponding auxiliary equipment beside the injection molding machine are reduced, and the space utilization rate is improved. In addition, due to the use of the central feeding method, a lot of stand-alone equipment is correspondingly reduced, which saves power and reduces maintenance costs. 3. Individualization: The central feeding system can meet different users, different workshop characteristics, and different raw material usage requirements. All can design the most optimized scheme according to actual needs. 4. Modern factory image: The central feeding system will reduce the pollution of raw materials and dust to the injection molding production to the lowest level, so as to maintain a clean production workshop. The central feeding system has a unique centralized dust recovery system that makes
|