Centralized feeding system design plan The vacuum feeder mostly adopts the vacuum suction method. The working principle of vacuum conveying is to form a certain negative pressure in the hopper cavity to make the material enter the hopper. The working process of the fully automatic vacuum conveyor is as follows: negative pressure is generated by a vacuum generator or a roots pump, and when the closed system reaches a certain vacuum, it starts to suck, and after the suction is completed, the material is discharged into the hopper, and the material is discharged. After a certain amount of preparation time has passed, the next cycle is performed. In this reciprocating cycle, the materials can always meet the material requirements of the equipment. The use and precautions of the vacuum feeder: Material particle size and shape, material conveying distance and material conveying height, Material feeding position, material density and material fluidity, etc. Material temperature, material sensitivity, material compatibility, The number of bending of the conveying pipe, energy consumption, material toxicity, flammable and explosive. A manufacturing factory limited company is mainly engaged in the design, production and sales of mechanical products. The products are mainly non-sexual, including handheld, desktop electronic, mechanical, electronic plastic toys, which are mainly exported to dozens of countries in Europe and America. The company plans a total of 17 injection molding machines for the material supply system in the A workshop. The raw materials used in this workshop are one type of ABS and two types of PP. There are three types of raw materials in total. The raw material packaging method is a 25kg raw material package. For bag cutting and feeding, customers only need to stack 3 kinds of raw material package cards in the designated position of the central raw material room. After the robot uses the vision system to determine the type of raw materials to be put in, the raw material package is then placed into the corresponding raw material barrel. Feeding. The material consumption of each machine in the workshop is 17kg/hr, and the total cooking consumption during the period is 289kg/hr. The feeding room is equipped with three 500kg raw material barrels (the material consumption of the second phase is reserved). Among the three kinds of raw materials, ABS needs to be dried and processed by the customer's current dryer.
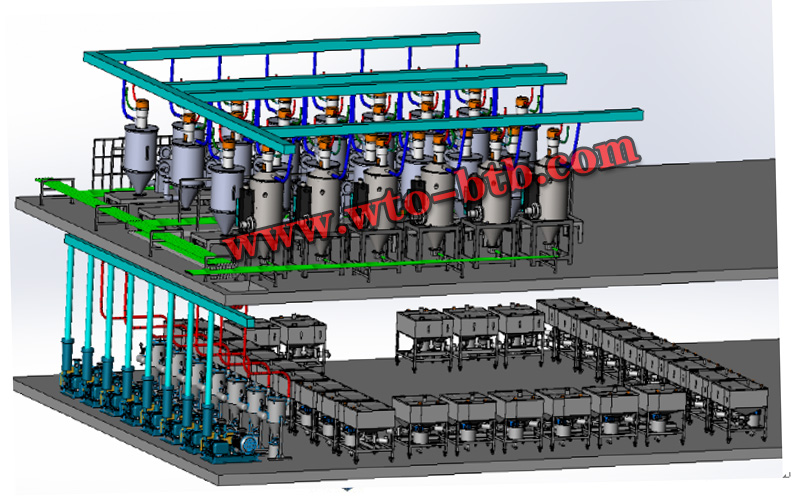 Design and scheme of centralized automatic feeding system For material supply, should I choose a system or a stand-alone machine? First of all, consider the production and use requirements, molding production process, product structure and processing performance. Secondly, consider the initial cost of the equipment, equipment area, energy consumption, stability during use, total operating costs for maintenance, and failure repair time. In the production process of plastic products, a lot of equipment is required. In addition to commonly used dehumidification, drying, and feeding, there are other process requirements equipment. Every production-oriented enterprise hopes that the commonly used equipment chosen is low in cost, high in efficiency, and stable in use. How to choose the best equipment? What is the difference between centralized transportation of plastic raw materials and single-machine transportation? 1. The most important feature of the system is high efficiency, labor saving, good stability, powerful expansion function, improved production site environment, touch operation more humanized, and unified unmanned management can be realized. 2. The centralized console can control one vacuum pump and multiple vacuum pumps to feed the injection molding machine at the same time. It can also monitor the external signals of the system and the working status of the system and possible faults in real time. There are many screening specifications, with reliable structure, strong excitation force, high screening efficiency, low vibration and noise, sturdiness and durability, convenient maintenance, safe use, etc. The centralized feeding system is widely used in mining, building materials, transportation, energy, and chemical industries. Product classification in other industries. The centralized feeding system is mainly composed of screen box, screen mesh, vibrator, damping spring device, base, etc. The vibrator is on the side plate of the screen box, and a motor is driven to rotate through a coupling or a belt to generate centrifugal inertial force, which forces the screen box to vibrate. The screen is the main wearing part. According to material products and user requirements, high-manganese steel woven screens, perforated screens and rubber screens can be used. There are two types of single-layer and double-layer screens. All types of screens can meet different requirements for screening effects. This series of centralized feeding system is seat installation. In any case, each series of vibrating screens play an important role in different fields. Full Speed Machinery will further tell you the main uses and characteristics of each centralized feeding system.
|