The heat balance method of the central feeding system 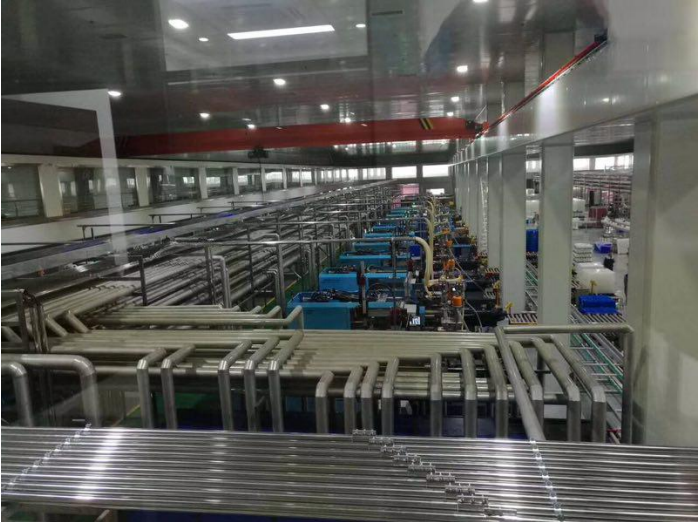 The central feeding system is designed for the production of plastic products in the injection molding workshop, realizing uninterrupted unmanned continuous molding operations. The variety of raw materials and the combined use of multi-color materials can be changed as needed to realize the automation of the coloring process. The system can regenerate and use the nozzle cold material in a fully automatic way, can control all the feeding equipment, and prevent the occurrence of blockage in the storage bin, and realize full automation by setting up a central monitoring station. The heat balance control of the central feeding system of the injection molding machine and the heat conduction of the mold are the keys to the production of injection molded parts. Inside the central feeding system of the injection molding machine, the heat brought by the plastic (such as thermoplastic) is transferred to the material and the steel of the mold through thermal radiation, and to the heat transfer fluid through convection. In addition, the heat of the central feeding system of the injection molding machine is transferred to the atmosphere and the mold base through thermal radiation. The heat absorbed by the heat transfer fluid is taken away by the hot air recovery system of the central feeding system of the injection molding machine. The purpose of controlling the central feeding system of the injection molding machine and the influence of the mold temperature on the injection molded parts. In the injection molding process, the main purpose of controlling the mold temperature of the central feeding system of the injection molding machine is to heat the mold to working temperature and to maintain the central feeding of the injection molding machine. The system mold temperature is constant at the working temperature. If the above two points are successful, the cycle time can be optimized to ensure the stable high quality of injection molded parts produced by the central feeding system of the injection molding machine. The speed of the central feeding system of the injection molding machine will affect the surface quality, fluidity, shrinkage, cycle and deformation of the central feeding system of the injection molding machine. Excessive or insufficient conveying mode of the central feeding system of the injection molding machine will have different effects on different materials. For thermoplastics, a higher conveying mode of the central feeding system of the plastic machine usually improves the surface quality and fluidity, but it will extend the cooling time and injection cycle of the central feeding system of the injection molding machine. The lower mold temperature of the central feeding system of the injection molding machine will reduce the shrinkage in the mold, but it will increase the shrinkage rate of the injection molded part after demolding. For thermoset plastics, a higher mold temperature usually reduces the cycle time, and the time is determined by the time required for the part to cool. In addition, in the plastic processing of the injection molding machine's central feeding system, a higher conveying speed will reduce the plasticizing time and reduce the number of cycles.
|