Central feeding system reduces the cost of plasticized fiber 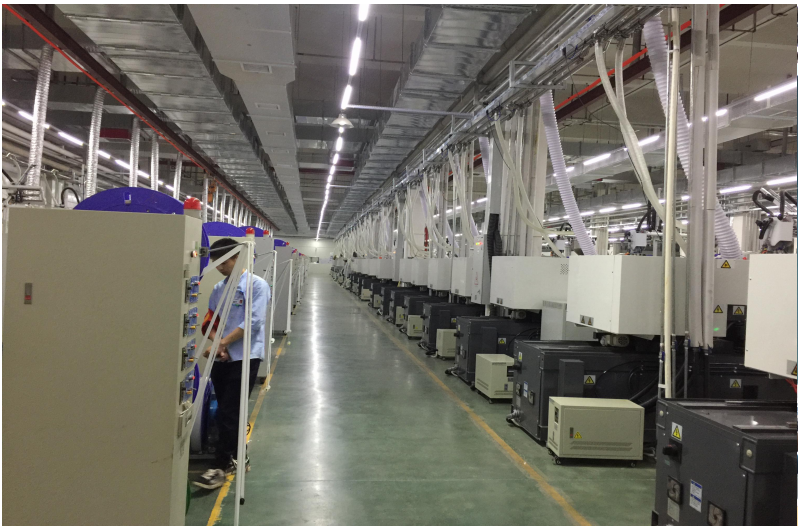 The plasticizing amount of extrusion plasticization has nothing to do with the screw diameter and screw length-to-diameter ratio, but only related to the two parameters of plasticizing time and speed. The limitation of diameter ratio, through the use of a central feeding system, can be used to achieve a large amount of plasticization with a relatively small screw, which creates conditions for the processing of large packaging containers with large weight by super plastic injection molding. The plasticizing injection volume is not limited by the screw diameter. The small-diameter extrusion screw achieves super-large plasticizing capacity. The injection is completed by a large-diameter plunger, which simplifies the mechanism, saves energy, and reduces manufacturing costs. Compounding plasticization is a pure plasticizing extrusion of the extrusion screw. During the entire plasticization process, the screw length-to-diameter ratio experienced by the plasticization of the material remains unchanged, and the plasticization quality is consistent. The use of a central feeding system overcomes the reciprocation of the conventional screw. The shortcomings of uneven plasticization quality caused by the change of the screw length to diameter ratio of the plasticized material of the plastic injection molding material ensure the consistency of the specific volume of the material in the molten state, and greatly improve the quality of the plasticization. The advantages of using a central feeding system in the injection molding workshop are: 1. Save energy 2. Save labor costs 3. Improve the company's overall image 4. Keep the factory environment clean and tidy 5. Centralized management of raw materials to avoid raw material waste and pollution 6. The transmission host can be isolated to reduce noise pollution The central feeding system adopts a vacuum conveying method. The plastic raw materials are transported from the storage tank to the central dehumidification and drying system through a centralized pipeline system, and then the dried raw materials are transported to each injection molding machine. The central feeding system adopts the design method of "one machine, one pipe" to ensure that the air in the entire system transports the raw materials and prevent the raw materials from regaining moisture after dehumidification and drying. At the same time, the conveying pipeline will be cleaned after each conveying cycle to ensure that there are no residual pellets in the pipeline, while avoiding the re-moisture of the raw materials, it also ensures the consistency of the properties of the raw materials added to the injection molding machine. Under the action of vacuum negative pressure, the original dust in the raw material will be filtered out through the dust filter system, which helps to improve the quality of the molded product.
|