The layout design of the injection workshop is a science that combines technology, economy and environmental protection. The task of the pre-design work is to conduct a comprehensive analysis of the design project, including process flow, production scale, main equipment, logistics, external conditions of the project, investment recovery period, land acquisition area for infrastructure, environmental protection, etc. The designer must go deep into the production site. Carry out necessary feasibility investigations and studies. The layout design of the injection molding workshop must meet the process requirements, the production process and the logistics direction are reasonable, the shared facilities and the layout of the whole workshop are coordinated, the output value per unit area is high, the relationship between people and the central feeding equipment, and coordination with other equipment, To facilitate equipment installation, repair and maintenance, further development of the production line, as well as energy conservation, environmental protection, safety, and lighting must also be considered. As the main content of the preliminary design of the workshop, the layout of the injection molding workshop is to reasonably determine the specific location of each component and its various equipment and devices. The workshop generally consists of six parts: production part, including various injection molding machines and auxiliary machines; auxiliary production part; warehouse part, such as raw materials, semi-finished products, and tool storage; aisles, including various main and auxiliary channels; management departments, such as production Offices, data rooms, quality control rooms, etc.; living parts, such as rest rooms, changing rooms, toilets, etc. The so-called reasonable arrangement is to make the movement of equipment, personnel and materials get close and effective coordination, not only can production activities be carried out effectively, but also can save production costs, and provide employees with a safe, comfortable and beautiful working environment.
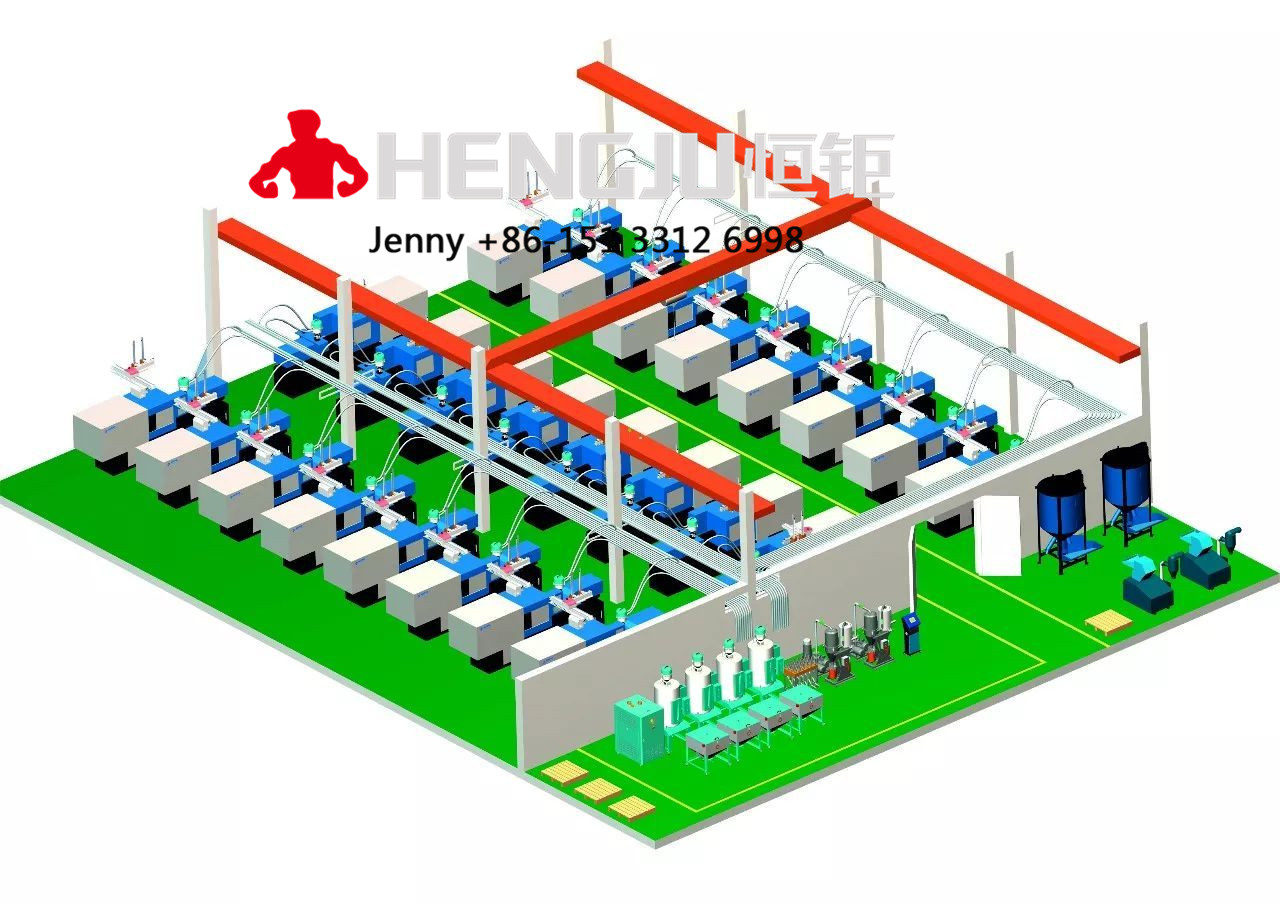 The following principles should be observed when designing the layout of the injection molding workshop: 1. Priority principle-shared equipment is the most concentrated equipment in workshop logistics, occupying the most Important roles should be placed first. 2. The principle of equipment grouping—according to the characteristics of injection molding production equipment, the grouping principle should be adopted for layout, and auxiliary equipment should be arranged according to The layout of units formed according to functional requirements can maintain logistics balance, reduce handling operations, and reduce Product and inventory, balance the role of equipment capacity and load. 3. The principle of production automation-injection molding machines are divided into manual operation, semi-automatic operation and fully automatic operation. For small For the injection molding workshop, since various auxiliary machines and facilities cannot keep up, it can only be operated semi-automatically, and there are no products. Consider the conveyor belt to inspect the packaging, and the product gate does not consider the crushing by the machine and the automatic feeding of the new material in proportion. Plastic machine hopper. But for large injection molding workshops, the production process automation and machinery should be designed as much as possible The raw materials should be automatically sent to the silo, automatically dried, and automatically sent to the feeding port of the plastic machine. When necessary, use a robot to take out the products, and the injection products are automatically transported, inspected, packaged and stored.
|